Kanban. Введение

Kanban. Введение
В начале XX века в США построили множество крупных складов. Вот почему в течение большей части XX века США опирались на крупное складское производство. Автомобильная компания могла построить 1000 автомобилей, а затем автомобили стояли на парковках, пока кто-нибудь не решит их купить. Но такая система не будет работать хорошо, если вы островное государство, как Япония.
Во-первых, найти место гораздо сложнее. Также дорого, для всех поставщиков задействованных в производстве автомобилей, покупать большие склады. Это все отнимает ресурсы. Помните, что производитель должен нести полную стоимость за выпущенную продукцию, поэтому автомобильный производитель может построить 1000 автомобилей, а затем может ждать месяцами, чтобы окупить свои инвестиции.
JIT (Just In Time) manufacturing (Производство точно в срок)
В 1960-х годах японские компании начали экспериментировать с так называемым JIT-manufacturing (точно в срок). Здесь производитель создавал автомобили в гораздо меньших партиях. Вместо 1000 автомобилей японский производитель мог сделать всего 100. Затем они брали эти небольшие партии и отправляли их напрямую в автосалоны. Им не нужно было беспокоиться о том, чтобы хранить их месяцами на парковке. В идеале эта система сокращала время от автомобиля до наличных денег. Он шел прямо от производителя к дилеру. Клиент мог даже купить его на следующий день, поэтому производитель нес меньше инвестиций. Вот почему это называется JIT. Продукт прибывает как раз вовремя для клиента.
Lean Manufacturing (Бережливое производство)
Система работала настолько хорошо, что японский автопроизводитель Toyota адаптировал ее для работы с их производственной системой. Они подправили ее и начали создавать новую версию, которую они назвали Lean Manufacturing. Одной из основных идей было то, что вместо того, чтобы «толкать» продукты в дилерские центры, они вместо этого должны были «тянуть» автомобиль через систему. Итак, когда клиент покупает до 100 автомобилей, это сигнал, что производитель должен построить новую партию.
Kanban (Канбан)
Идея о «тянущей системе» против «толкающей системы» стала центральной идеей Канбана. Канбан объединяет Lean Manufacturing с практикой, которая использовалась в японских продуктовых магазинах. Фактически, слово «канбан» означает на японском языке «сигнальная карта». Карта канбана была сигналом для продуктового магазина, что им нужно заказать новые продукты. Система использует эти карты канбана как способ сигнализировать о необходимости “затянуть” больше продуктов в конвейер.
Так, если было 40 банок супа, а осталось только 10 банок, они клали красную карту канбана рядом с банками супа. Затем менеджер проходил по магазину и заказывал все, что имело красную карточку.
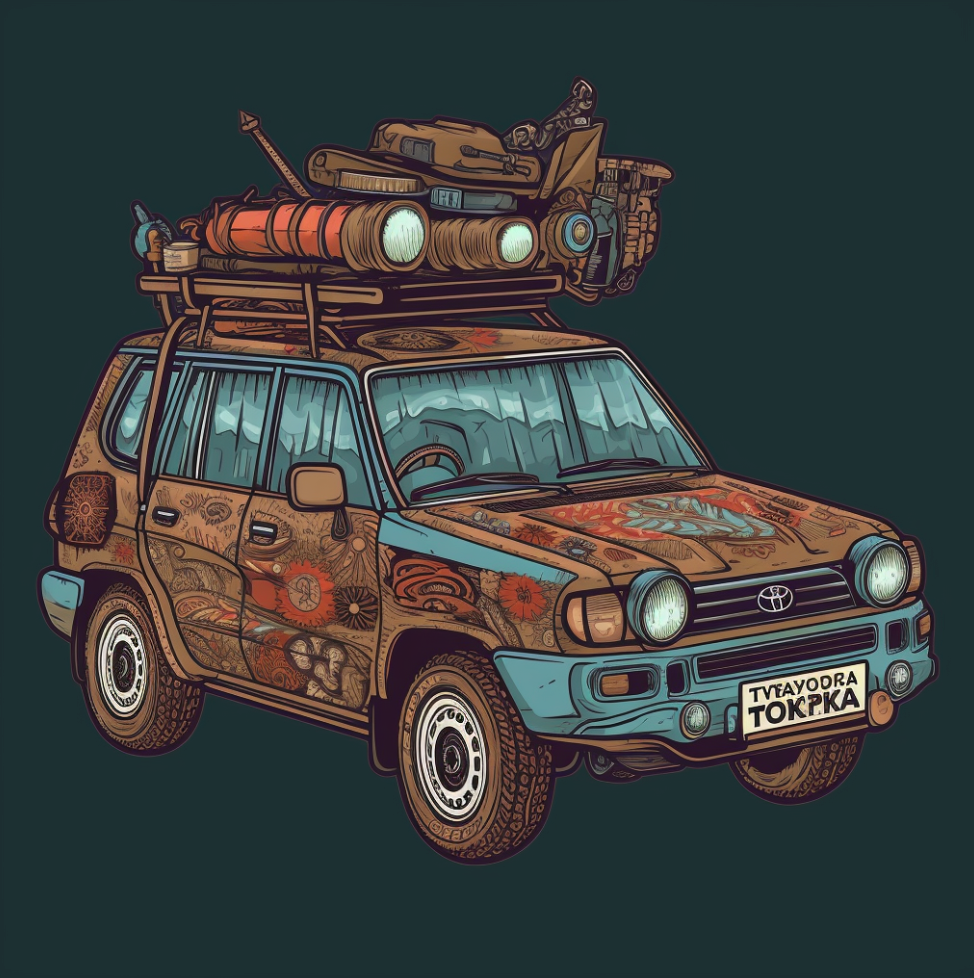
Toyota Production System (Производственная система Toyota)
Производственная система Toyota смешала эти практики канбана с Lean Manufacturing. Они могли использовать эти карты, чтобы показать, когда запас автозапчастей становился низким. Toyota могла нуждаться в 100 автомобильных сиденьях для сборки своих автомобилей, поэтому они могли положить карту канбана рядом с автомобильными сиденьями, когда они достигали критического уровня. Таким образом, Toyota «тянула »/заказывала новые автомобильные сиденья от своего производителя. Это также позволило Toyota не хранить лишние сиденья на производственной линии, что помогло производителю автомобильных сидений убедиться, что они строят именно то, что нужно клиенту.
Доставка продуктов
Теперь, в начале 1990-х годов, консультант Дон Райнертсен начал писать о том, как использовать эти же концепции для разработки продуктов. Вместо того, чтобы использовать Lean Manufacturing для сборки автомобилей, он сказал, что вы можете использовать его для доставки продуктов. Хитрость заключалась в том, чтобы доставлять их небольшими партиями и как можно лучше управлять этим размером партии или очереди. Идея заключалась в том, чтобы держать очереди небольшими и минимизировать время, которое продукт проходит через вашу систему. Таким образом, вы могли предсказать, сколько вам нужно, чтобы получить готовый продукт.
Преимущества использования Kanban и JIT(Just In Time) - manufacturing
- Уменьшение времени от заказа до получения продукта.
- Повышение эффективности производства.
- Сокращение затрат на хранение и транспортировку.
- Улучшение качества продукции.
- Увеличение удовлетворенности клиентов.
Недостатки использования канбана и JIT-производства
- Сложность внедрения и настройки системы.
- Требуется четкая и прозрачная система коммуникации между всеми участниками процесса.
- Не подходит для всех видов производства.
Далее мы продолжим погружаться в методологию Kanban и следующая тема “Kanban и настройка емкости работ”.
Комментарии 0
Авторизуйтесь чтобы оставить комментарий
САРЖАН М · Окт. 17, 2023 00:06
Kirill +
Kirill Grebennikov · Окт. 14, 2023 14:05
Очень интересный обзор преимуществ и недостатков использования Kanban и JIT в производстве. Особенно впечатляет, как эти методики могут существенно оптимизировать рабочие процессы, делая их более эффективными и отзывчивыми к потребностям клиентов. Однако, как и любой инструмент, его применение требует осмысленности и учета специфики каждого предприятия. С нетерпением жду дальнейших материалов по теме!